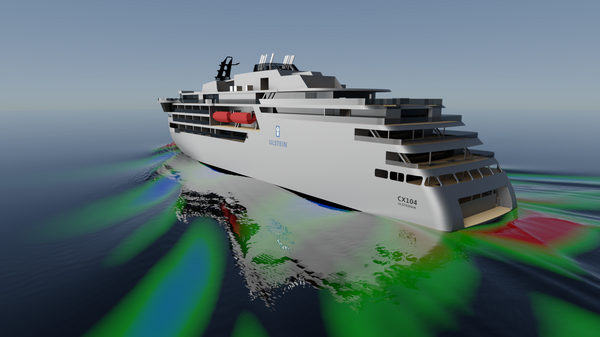
CFD simulations
Computational Fluid Dynamics, abbreviated as CFD, is in its general meaning a numerical analysis simulation tool for engineers and researchers to help solve problems that involve fluid flows.
Harness the power of CFD
Typical and well-known industrial applications are simulations of air around cars or aircraft. Within these applications, CFD has, over a few decades, helped design much more efficient and comfortable products.
It is also an increasingly popular tool within the marine industry, where model-scale experiments have long been the standard. With increasingly more powerful and less costly computers, CFD can be a very useful complement to experiments. In some cases, CFD can even replace experiments due to matching accuracy at both lower cost and shorter time to results.
At Ulstein Design & Solutions, CFD is used daily to predict calm water hull resistance. In the design evolution, hull lines and appendages are designed and aligned for the lowest possible hull drag.
Navigate with confidence
Since calm water is a sea state that ships rarely encounter, it is important to design a ship that operates well in waves. This is related to fuel consumption as well as comfort for crew and passengers.
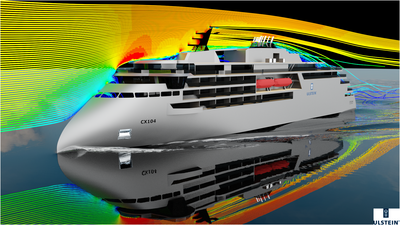
Beyond hydrodynamics
Since calm water is a sea state that ships rarely encounter, it is important to design a ship that operates well in waves. This is related to fuel consumption as well as comfort for crew and passengers.
At Ulstein, CFD simulations are not only an internal activity or restricted to the marine industry. We have in-house CFD software and powerful computer hardware to solve your flow challenges.
Do not hesitate to contact us if you have any questions!
Get in touch
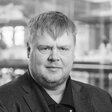
Roy Lindset
- Description
- Manager service dept.
- Affiliation
- Ulstein Design & Solutions AS