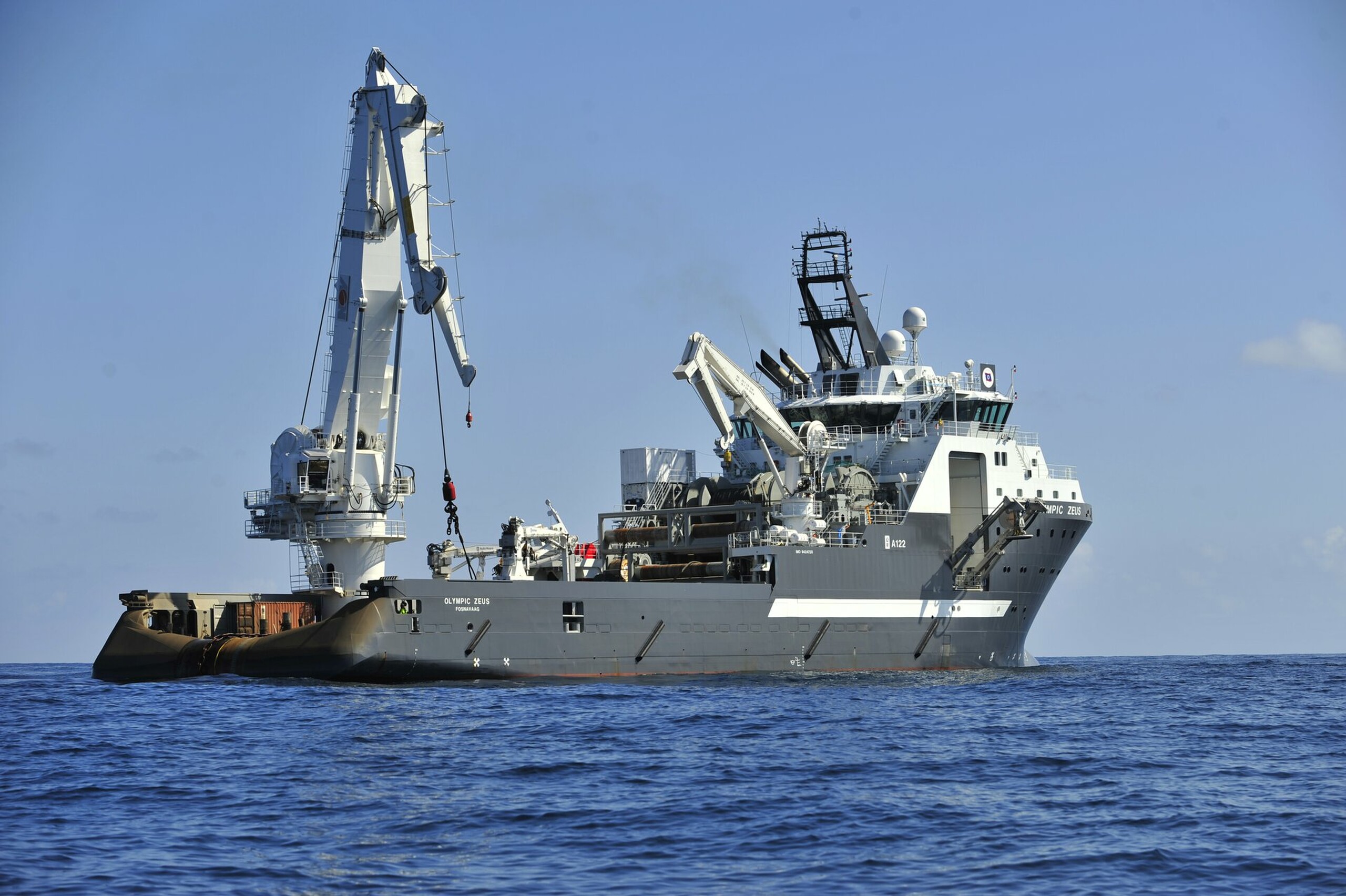
Olympic Zeus: A Pioneer in AHTS Hybrid Propulsion
By adopting hybrid Diesel-Electric/Diesel-Mechanical (DE/DM) systems, unlike its predecessors that relied solely on Diesel-Mechanical (DM) systems, the Olympic Zeus captured significant attention in the AHTS market upon its delivery in 2009. This innovation led to an impressive fuel consumption reduction of up to 70%.
The Olympic Zeus is a state-of-the-art vessel, designed for a variety of operations, including towing, anchor handling, subsea, supply, survey, crane, and ROV operations, as well as general offshore construction work. It is groundbreaking in many respects, including the hybrid machinery, deep-water capabilities, excellent seakeeping, and performance characteristics that ensure outstanding fuel economy and low emissions.
Hybrid propulsion innovation revolutionised the AHTS market, significantly benefiting the environment
The Olympic Zeus was the first anchor handling/construction vessel with a diesel-mechanical/diesel-electric hybrid propulsion solution that was designed to primarily operate in diesel-electric mode. The hybrid propulsion system on this vessel is a groundbreaking innovation and was nominated for the Green Ship Technology Award.
According to Runar Stave, Senior Vice President of Olympic Shipping,
From our experiences in the North Sea, we see that the Olympic Zeus runs diesel-electric 80% of the time. Figures showed that fuel consumption in these modes was about 50% lower than for most competing vessels due to the hybrid solution.
After a number of jobs, we’d proved to the market that we can, on average, run the ship on 30% of the fuel of a conventional diesel anchor handler, and save up to 70% in some operation modes compared to a conventional, diesel-mechanical ship.
The propellers can be driven directly by the diesel engines or by electric motors powered by generator sets, and the two modes can also be combined in hybrid mode for maximum performance.
The system is tailor-made to fit the vessels’ dynamic and versatile work operations.
Being fuel-efficient reduces emissions
The three key elements that provide the system with unsurpassed dynamic capabilities and low fuel consumption are:
- Powerful Electric Propulsion:
- This allows most vessel operations to be performed in diesel-electric mode, with very slow rotating main propellers in electric mode, eliminating zero pitch losses.
- User-Friendly Interface and Advanced Automation:
- These fully utilize the dynamic nature of the hybrid propulsion concept, making it efficient and easy to operate.
- Selective Catalytic Reactors and Compliance:
- The vessel is equipped with selective catalytic reactors to meet IMO requirements and fully complies with DNV’s Clean Design Criteria, ensuring reduced emissions and environmental impact.
A hybrid vessel has high fuel-saving potentials
Hybrid vessels, unlike DM vessels, can run on fewer engines with higher load and optimum fuel efficiency, leading to significant fuel savings and reduced emissions.
While DM vessels need much propulsion power for all operations, a hybrid vessel has high fuel-saving potentials. Given that the vessels only require low or medium propulsion power most of the time they are in operation, they can run on fewer engines, with higher load and optimum fuel efficiency. Only a few vessel operations require the extra power from the hybrid solution, leading to thousands of litres of reduced fuel consumption every single day.
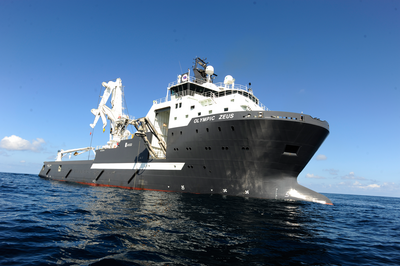
"It was a comprehensive job, developing an AHTS that is fully designed around energy efficiency in daily operations at low power loads, having the massive bollard-pull benchmark capability only as a side note. A completely different design strategy compared to the classic mechanical AHTS, were everything was about gaining the massive bollard-pull figure at a lowest possible price.
"The turning point came from analysing data during a rig move west of Shetland. We were surprised by the amount of waiting and idling, and the low power levels used even during anchor handling operations. This insight led us to change our approach to developing the new generation AHTS.
We had to accommodate the nature of a high bollard pull ship, with large diameter propellers, main gears, and a significant diesel engine power station. We designed the propellers to run at very slow RPMs in diesel-electric mode, maintaining high torque capabilities. Additionally, the electrical power station was designed with five smaller generator sets, allowing us to scale down the power station to match actual electrical loads, ensuring engines run efficiently at optimal loads.
This electrical mode was intended to operate within a bollard pull range up to 150 tons. When exceeding this, a seamless shift to hybrid mode can be performed without reducing propeller thrust. Based on the operation profile from the field trip, we estimated that the anchor handler could operate in electric mode up to 80% of the time.
We initially expected to save 25% in energy consumption, but the results exceeded our expectations. We more than halved the energy consumption for this type of vessel in AHTS operations, significantly impacting fuel savings and emissions, says Frode Sollid, system architect.
Clients could not believe such low numbers were possible
The feedback from clients of the Olympic Zeus was overwhelmingly positive. Many expressed amazement at the vessel’s remarkably low power requirements, stating they couldn't believe such low power consumption was possible,
said the Captain of the Olympic Zeus.
Being the first mover in hybrid solutions for the AHTS market, Olympic welcomed the other hybrid vessels entering the market. "This is all the better for the environment,” concluded Runar Stave.
Cutting-edge design and capabilities
The vessel is based on the ULSTEIN A122 design by Ulstein Design & Solutions AS and constructed by Ulstein Verft. It measures 93.8m in length, 23m in width, and 10m from the main deck to the keel. With a bollard pull of approximately 260 tonnes, the vessel can be equipped with a 250-tonne heave-compensated offshore crane and two A-frames of different types. Its large dimensions and additional onboard power makes it particularly well-suited for deepwater operations.
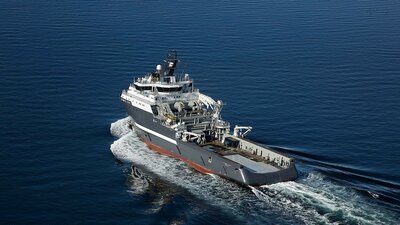
We chose Ulstein because we had great faith that it could deliver a ship of this complexity. The decision was based on the excellent performance of the previous Ulstein-designed and built ships, the ULSTEIN A101 anchor handlers, Olympic Hercules and Olympic Pegasus, delivered in 2002. We were very pleased with those vessels, but the trend shifted from operations at depths of 1,000–1,500 metres to advanced subsea operations down to 2,000–4,000 metres. To provide the best services for the current market, we needed even larger ships with advanced capacities,
said CEO Stig Remøy, Olympic.
The Olympic Zeus represents a significant advancement in hybrid propulsion technology and have set new standards for fuel efficiency and environmental performance in the maritime industry.
Related articles
Celebrating the Olympic Zeus: A pioneer in AHTS hybrid propulsion
The Olympic Zeus, launched in 2009, introduced a hybrid power system, reducing fuel consumption by up to 70%. After reaching its 15th anniversary in 2024, it continues to set new fuel efficiency and environmental performance standards.
Anchor Handling Tug Supply
Our Anchor Handling Tug Supply (AHTS) are characterized by a hull and an engine/propulsion system configuration that secure maximized bollard pull and fuel efficient operations.
Olympic Zeus
Able to work as an anchor handling vessel and as an offshore support vessel, with a large 250t crane for performing heavy subsea construction & installation jobs. It is equipped with a hybrid configuration of power plants, with two main propellers, one retractable thruster forward, two side tunnel thrusters forward, and two aft.