«Ulstein has its own yard, and the ship designers can follow the shipbuilding process directly. They can inspect the vessel while it is being built, participate in the sea trials, and receive feedback from the ship owners via the shipyard after the vessels have entered into operation. Feedback is actively used to improve the ship designs, which is a win-win situation. This is what we call incremental - or stepwise - innovation», explains Tore Ulstein, head of the board of Ulstein.
«The owner's feedback and Ulstein's shipbuilding experience are of essential value when ship owners decide to have their newbuild constructed at other yards, such as Brazil, China or South Korea, countries where several Ulstein-designed vessels have been built. Ulstein can follow up on every part of the project process, from initial design sketches, basic design, and engineering, to equipment purchases, main equipment deliveries, electrical installations, site follow-up, pre-commissioning, commissioning, sea trial and testing. We have the complete service line in-house», states Tore Ulstein.
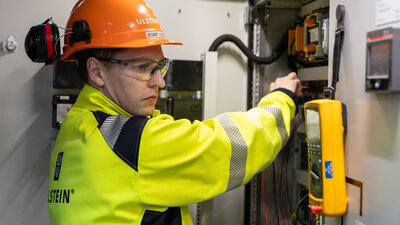
Disruptive innovation in problem solving
«Equally important is the role the ship designers in Ulstein take in radical - or disruptive - innovation», he says, and continues:
«This comes as a result of dedicated project work to solve a problem or issue raised by the ship owner or the end-user. The issue is handled through an ABD (Accelerated business development) process in which the ship owner is an active part of the problem-solving process, combined with data from field studies, market studies, and other insight documentation.
A recent example is the concept design of a novel trawler, ECOFIVE, where Ulstein has cooperated with Bluewild. The ship owner contributed with their experience in fishery, while Ulstein contributed with design and engineering experience, field studies and research. The harvesting methods on this innovative, award-winning trawler are less damaging to the catch, resulting in increased quality of the end product. Watch an informative animation here. The hull and propulsion solutions provide for reduced fuel consumption and less emissions to air».
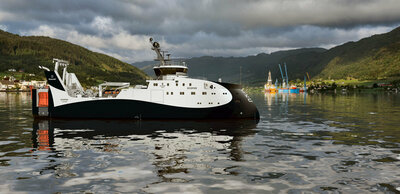
Turned the bow upside down
Radical innovation can also arise from the designers' initiatives. One example, well-known to the market, is the backward-sloping bow, the X-BOW®:
«Introduced in 2005, the bow has now been implemented in more than 100 vessels of various types. The X-BOW provides smoother travel in head seas, resulting in a consistent transit speed and higher operability in adverse sea states. Referring to our history of design and equipment packages for yards outside our own yard, more than 70 of the first 100 X-BOW vessels have been contracted at other yards, demonstrating the value of our design offer», says Tore Ulstein, and continues:
«Furthermore, a derivative of the X-BOW, the aft solution X-STERN®, holds much of the same design thinking and benefits to the vessel. The sloping, higher stern allows for a sharp stern shape in which a pointed aft replaces the transom plate. Some of the benefits are improved safety for crew and equipment, increased flexibility in operations and significantly reduced fuel consumption».
Another derivative is the TWIN X-STERN®, as seen in the illustration below, with main propulsors fore and aft.
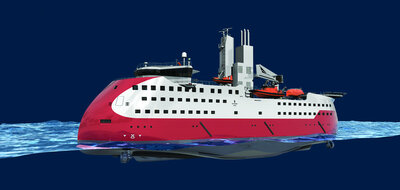
Hybrid propulsion for AHTS
Ulstein also mentions another example, the development of the hybrid propulsion concept for anchor-handling tug supply vessels. «The concept combines higher efficiency and better performance at high loads and excellent fuel consumption at low loads. The medium-sized diesel-mechanical and diesel-electric systems in Olympic Zeus and Olympic Hera were combined into one large hybrid propulsion system, which needs less space and is less expensive than a large diesel-electric system».
The Olympic Zeus experienced a reduction in fuel consumption by 70 per cent: Celebrating the Olympic Zeus: A Pioneer in AHTS Hybrid… | Ulstein
Ulstein has 100 years of history and decades of design experience. Tomorrow awaits.