Growing demands and weighty consequences
The offshore wind market has experienced exponential growth. Turbines have grown taller, and the distance from wind farms to shore has increased. Consequently, the cable length required for each wind farm has escalated significantly. The weight of these cables—once an afterthought—now poses a critical challenge.
Distribution of CLV activity by market
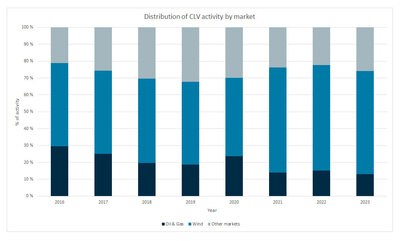
Inadequate cable vessels lead to delays and cost overruns, threatening the viability of renewable energy and our sustainable future.
How cable weight has changed in offshore wind industry
When examining the cable length and associated weight across windfarms globally, it’s observed that 75% of installations in the 2010s were equipped with export cables weighing under 7,000 tonnes. To achieve this same figure for windfarm projects in the 2020s and 2030s, the cable weight jumps to 13,000 tonnes. For installations representing 90%, there’s been an increase in cable weight from 13,000 tonnes in the previous decade to 18,000 tonnes now.
It is anticipated that the upcoming generation of export power cable laying vessels will need a capacity of 20,000 tonnes to manage installations at the largest windfarms with a single cable load.
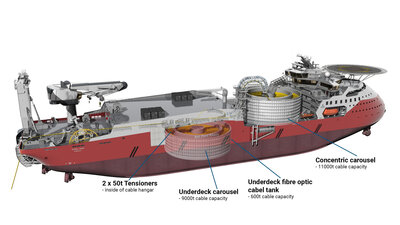
Why the ULSTEIN SX225 is a game-changer
- A design tailored for tomorrow
- The ULSTEIN SX225 stands at the forefront of innovation. With a staggering cable capacity of 20,000 tonnes, it can handle the largest wind farms with a single load. This vessel isn’t just about size but efficiency, precision, and adaptability.
- Dual carousels - a symphony of storage
- The vessel’s cable storage system is ingeniously divided into two carousels. An 11,000-tonne carousel efficiently manages cables on deck, while an additional 9,000 tonnes are stored below deck. This dual-carousel setup ensures seamless cable handling during installations.
- ULSTEN TWIN X-STERN - navigating the elements
- The ULSTEIN SX225 features the groundbreaking ULSTEN TWIN X-STERN design. Six azimuth units—three forward and three aft—provide exceptional dynamic positioning (DP) capability. The TWIN X-STERN platform is also a prerequisite for operating in shallow waters on high DP capability. Imagine a vessel that dances with the waves, maintaining stability even in challenging conditions.
- ULSTEIN SX225 - a vessel for global energy connectivity
- The ULSTEIN SX225, renowned for its efficient wind farm-to-shore connections, serves a dual purpose. It facilitates power transmission from wind turbines to land and is vital in laying intercontinental power cables, reinforcing global energy networks and fostering a greener future.
- Net Zero Ready - pioneering sustainability
- The ULSTEIN SX225 is not just mere functionality. It is Net Zero Ready, prepared for dual fuel operation with methanol. The vessel has two battery rooms, each initially equipped with 1,100 kWh of battery capacity—spinning reserves and peak shaving in action.
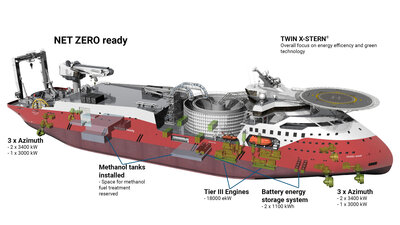
Charting a greener course
The world’s need for clean electricity is more pressing than ever as we face the challenges of climate change and the transition towards renewable energy sources. The ULSTEIN SX225 is designed to be a significant player in this transition. It's a large platform with increased operability that serves a dual purpose.
The SX225's capabilities in supporting the offshore wind industry and its contribution to power global connectivity underscore its role as an embodiment of a commitment to a greener future.
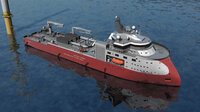
Designs that move the industry forward
Explore our portfolio of cable-laying vessel designs.
Learn more about cable laying vessels
Cable Laying Vessels
Committed to delivering thoughtful vessel designs, we prioritize safety, crew comfort, and operational efficiency at a cost-effective rate. Experience the next level of industry advancement with our dependable cable-laying portfolio, where we offer continuous support throughout your vessel's lifecycle.
Why is the X-BOW particularly well suited for Cable laying vessels?
With an ULSTEIN X-BOW® Cable Laying Vessel, vessel motions will be reduced and, consequently, also the strain on the cable. This might allow operations in worse weather conditions than a vessel with a conventional bow. Due to the absence of whipping movements in the ship, there will be less wear and tear of the cable.