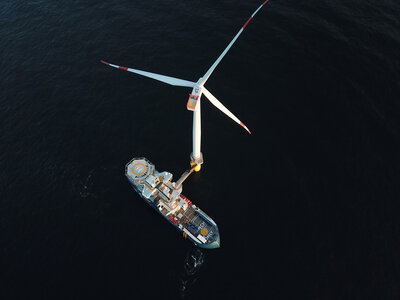
Before the introduction of active motion-compensated personnel transfer gangways, technicians were primarily transferred to turbines via small crafts, requiring them to climb ladders. These transfers are often restricted by wave conditions.
With the W2W gangways, service can now be performed in rougher seas, significantly increasing operational days by weeks, even months, each year.
Despite this advancement, Crew Transfer Vessels are still widely used as an additional method, enhancing an Offshore Wind Vessel's capacity to service more turbines in a single day.
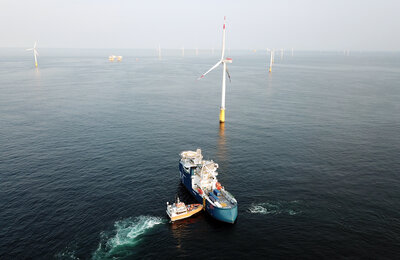
A large number of successful transfers
After 16 months of service, the SOV vessel Windea La Cour, a 2016 delivery, had successfully completed several thousand transfers at the Gemini offshore wind park. "The vessel has proven to be highly efficient, with the X-STERN and X-BOW designs reducing slamming and spray to maintain comfort," commented Matthias Müller, managing director at BS Offshore.
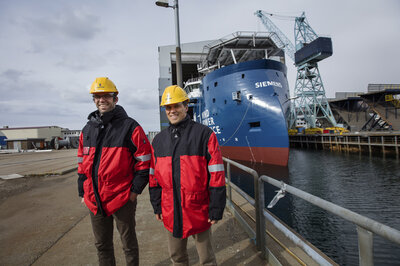
Technicians have fortnight shifts
As offshore wind farms are established further from shore, overnight stays become necessary. The Service Operation Vessel (SOV) Windea La Cour accommodates around 40 technicians for two-week rotations. This vessel services the 150-turbine offshore wind farm Gemini off the Netherlands and has been chartered by Siemens on a 15-year maintenance contract, lasting until 2031. Technicians bring pre-packed lunches and remain on the turbines until their shift ends or maintenance is completed, requiring transfer to another turbine. The workdays are long and can be intense; weather permitting, technicians work up to 12 hours a day for 14 consecutive days.
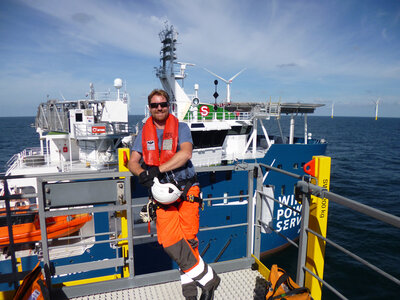
On-board spare part supplies
A crucial part of the job for service technicians is waiting for the delivery of spare parts. Nowadays, the vessel carries almost everything needed to maintain the wind park. Once the required spare part is identified at the turbine, the technicians call the vessel, and the part arrives within an hour. If the rare event that the spare part is not on board, the daughter craft can be dispatched to the Eemshaven base, approximately 85 kilometres away, to retrieve it. Every 14 days, the vessel returns to Eemshaven to change the team of technicians and replenish supplies.
High standard keeps up spirits after long shifts
Returning to the vessel at the end of a long day, the high comfort on board soothes both body and mind. Each technician has a single cabin with heated bathroom floors and their own satellite TV. The cabins are free from engine noise, thanks to the BLUEDRIVE PlusC electric propulsion system from Siemens, combined with the X-BOW fore part and X-STERN aft from Ulstein, which help keep noise, vibrations, and movements to a minimum.
Food as the social hub
The mess is the natural gathering place for everyone on board. Hot meals are served twice daily, and food and sweets are readily available. The high-class chefs, delicious food, and conversation around the dinner table are vital aspects of social life. The vessel also offers a cinema, a spacious and well-equipped gymnasium, an outdoor Jacuzzi, and a sauna for ultimate relaxation. This high comfort level is essential for everyone working and living on the vessel for half the year.