How knowhow reduces LCOE in offshore wind
Many new offshore wind farms are located further from shore, often in deeper waters and rougher conditions, and feature ever-larger wind turbines. This leads to development of new ships that can handle the new requirements these fields and turbines pose.
Companies that rely on ocean-going vessels are under pressure to reduce their environmental footprint. In addition to the IMO target, the European Parliament has voted for a similar reduction. The demand for greener vessels for offshore wind farms is expected to increase with the growth of the offshore wind market, which is projected to reach USD 1 trillion by 2040.
ULSTEIN provides ship designs, system solutions and services for efficient and reliable marine operations. This includes ship designs for all cycles in the life of the offshore wind farms, with solutions for environmentally friendly vessels to serve the various stages.
The first phase - planning and development
The seabed survey and meteorological data gathering are essential for designing the substructures and selecting wind turbines.
The survey tasks during this phase are often done by various actors using different types of vessels. Ulstein has an extensive track record in designing and constructing offshore support vessels capable of performing these tasks, including environmental, geophysical and geotechnical surveying.
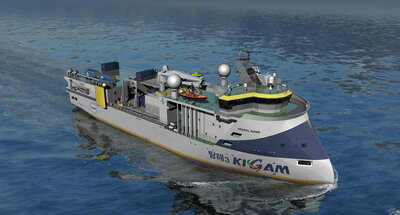
Phase two: Substructure installation
The construction of offshore wind farms starts with preparing the seabed for the main infrastructure and installing foundation structures.
Cable laying vessels (CLV) are essential in installing new offshore wind farms. Ulstein has developed CLV designs for the installation of both transmission cables and array cables. All the CLV designs in the ULSTEIN SX series are designed with the patented ULSTEIN X-BOW®. The X-BOW minimises the accelerations, leading to smoother motions and reduced fuel consumption in waves. It also diminishes the jerking and wear-and-tear of the cables. The hull is optimised for the vessel's actual speed range as initial CFD studies can be performed to reduce wave resistance and verify power requirements.
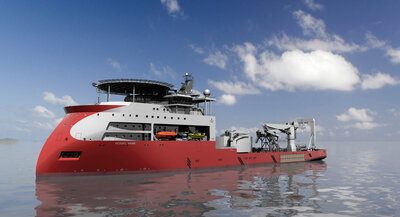
Subsea Rock Installation (SRI)
The next step is Subsea Rock Installation (SRI) to lay protective rock coverings around turbine foundations to avoid scouring. Ulstein holds a position as the world-leading ship designer in SRI new builds. SRI vessels are essential for cable and substructure protection. Our latest design in this field will be the first U.S.-flagged and Jones-Act-compliant vessel of its kind and the first for the U.S. offshore wind industry. Contracted by Great Lakes Dredge & Dock (GLDD), the vessel is currently being constructed by Philly Shipyard.
The American Bureau of Shipping (ABS) reviewed and approved the design, which is being built with best-in-class safety and low emissions standards (LEV, Sustain2). To reach the low emission and sustainability goals, the vessel design includes EPA Tier 4 engines, plug-in shore power connection for loading in ports and battery packs for peak-shaving. The vessel can also run on biofuel to reduce its CO2 footprint and is equipped with active emission control technology to minimise NOx emissions. In the concept phase, the Ulstein Blended Design method enhanced cargo efficiency, boosted the GLDD business case, and reduced overall fuel consumption.
Ulstein's track record in SRI vessels also includes Van Oord's 'Bravenes' vessel and DEME Offshore's 'Flintstone' vessel.
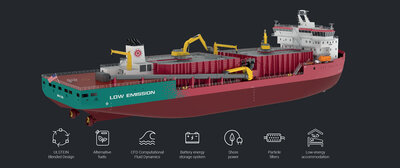
Phase three: Installation & Commissioning - Putting the pieces together
Offshore heavy lift vessels are one of the design areas that Ulstein specialises in. Given the trend in the industry for ever-bigger wind turbines, larger installation units will be required for both foundations and wind turbines. With new offshore wind farms also more often being established further from shore, transit times become longer, and the size of vessels must be optimised for these new conditions.
HLV and feeder vessels
Wind turbine foundations are installed and topped with a transition piece to provide the basis for the wind turbine's tower. This operation is carried out by heavy lift vessels (HLV) with crane capacities of at least 3,000t. Heavy lift and feeder vessels transport turbine components and foundations from manufacturing ports to marshalling hubs and offshore wind farms.
Jack-ups
With the dawn of the new 15-17MW offshore wind turbines, installation capacities of the current third-generation wind turbine installation vessels will be pushed to the limits and beyond. Self-propelled jack-ups are the chosen tool for installing wind turbines as they provide more precision when handling the nacelle and turbine blades. A new generation of jack-up vessels is necessary to serve the future offshore wind industry. The X-JACK series can handle these parts with the necessary precision and without the negative effects of waves and currents. The X-JACK design cuts up to 25 % in installation cost compared to currently available jack-ups.
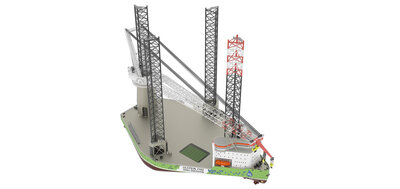
The X-JACK design driver is to significantly increase the efficiency compared to existing units in the market, both in logistical layout and in payload capacity, while being lighter at the same time. The combination of an innovative hull shape and vessel layout with well-proven jacking and crane technologies from reputable suppliers provides unrivalled heavy lift and cargo capabilities.
The X-JACK concept is scalable and includes three versions: J104, tailored for maintenance and exchange of wind turbines/nacelles; J102, sized for the most optimal and cost-effective turbine installation; J103, designed to carry and install six next-generation wind turbines to realize even the world's most remote wind farm locations. Read about the ULSTEIN X-JACK initiative.
Turbine start-up
Installation vessels are accompanied by construction support vessels providing the necessary services for the commissioning and start-up of the turbines.
One example is the 'Seaway Alfa Lift' vessel for Seaway 7. The heavy-lift crane installation vessel with semi-submersible heavy transportation capabilities is the world's largest, custom-built vessel for offshore wind foundation installation, featuring a 3,000-tonne crane and more than 12,300 square metres of available deck space.
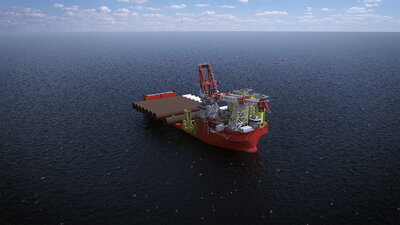
Because of the 'Seaway Alfa Lift' capacities and capabilities, Seaway 7 has been awarded the transport and installation of monopile foundations and transition pieces for the Dogger Bank wind farms.
"We need new entrants that can think differently and make the industry even more competitive"
Halfdan Brustad, Vice President Equinor's Dogger Bank
The main deck incorporates a fully automated skidding system, whilst the forecastle deck carries transition pieces and mission equipment. The monopiles that will be installed at Dogger Bank will be amongst the largest ever used on an offshore wind farm. Utilising one single vessel, the foundations will be transported to the offshore site, approximately 130km off the northeast coast of England, and installed in water depths of up to 35 metres. The 216-metre vessel will load out 10 Dogger Bank monopiles and 10 transition pieces for installation at a time thanks to its 48,000-tonne deadweight.
Performing the work of two vessels in one, the 'Seaway Alfa Lift' is optimising efficiency for the transport and installation of next-generation foundations.
Phase four: Operations and maintenance
This phase includes the daily routines of inspection, maintenance and service of the offshore wind farm. Any downtime on the turbines represents lost revenue. Therefore, it is important that service personnel can access the wind farms quickly and with spare parts and tools available close by.
The hull line designs X-BOW® and X-STERN® have proven to improve workability, safety and comfort. Both significantly reduce slamming and vibrations caused by waves in head seas.
Ulstein was one of the first ship designers to take on the new challenges presented by the offshore renewable energy industry when it designed the "Siem Moxie" (now "Seaway Moxie"). At the time, this was the first purpose-built walk-to-work vessel ordered to assist in cable termination and testing during the construction of a wind farm.
Walk-to-work was soon adopted for service and maintenance of turbines, introducing a new vessel type, the (Construction) Service Operations Vessel or (C)SOV.
When designing its first SOVs, Ulstein questioned ship masters about how they prefer to operate the vessels at the wind farms. The majority reported that they prefer to manoeuvre stern first for in-field operations, for which they gave various reasons:
- All work is being performed from the aft deck. Keeping stern first leads to a better overview of the vessel's positioning, as the gangway, turbine and ship's side can all be observed from the operations bridge.
- Furthermore, most thrust power is installed in the aft part of the vessel, enabling it to keep positioned more easily, and the vessel doesn't have to turn around before moving to the next turbine, saving manoeuvring time between turbines.
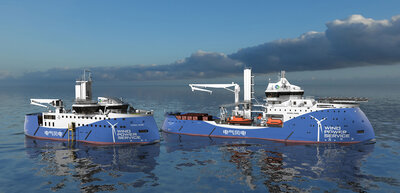
The X-STERN
The X-STERN was introduced in 2015 and was awarded the Next Generation Ship Award by Nor-Shipping, recognising the most promising design among the ships that will be at sea in the coming decade, demonstrating the most significant advances and innovations in design. The design has been assessed for energy efficiency, innovation, suitability and flexibility, utilisation of technology, safety and security and environmental sustainability. The X-STERN proved very valuable for SOVs operating astern regularly. Several X-STERN new build vessels have been delivered from Ulstein Verft, and more are planned for construction internationally.
The crews on X-STERN vessels report additional benefits
The X-STERN is kept towards the weather while on standby during the night. The service crews get complete rest in between their maintenance shifts due to no slamming or vibrations.
There is no slamming due to the X-STERN, even when transferring between turbines.
If the weather is not too adverse, the ship stays on the spot with only two thrusters running, which substantially reduces fuel consumption during stand-by.
The X-STERN hull also provides significant fuel savings. Findings show that the X-STERN results in up to 60 per cent less power required when manoeuvring stern first compared to a flat transom stern.
Also, read the story of the senior DP operator on the first X-STERN Service Operation Vessel.
Next-generation service vessels
Ulstein has a clear ambition of being at the forefront of the technology development required to achieve zero-emission offshore operations. One important design aspect is our innovative hulls, including our novel TWIN X-STERN. These ships leverage the advantages of the X-STERN by creating an underwater hull shape that is bi-symmetrical with two main propeller units in each corner, ideal for offshore operations requiring continuous positioning. The TWIN X-STERN is more manoeuvrable, with low noise for increased comfort and the potential to save energy.
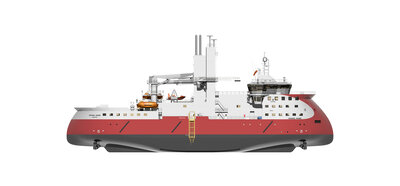
High performance is achieved with the minimum required power by having excellent performance in any direction and more efficient utilisation of the thrusters. The result is significantly more effective operations and reduced energy consumption, which is the key to performing vessel operations with reduced emissions.
To lower the vessel's environmental impact further, moving towards zero-emission, Ulstein is preparing future-proof power solutions. Ulstein's (C)SOVs can be delivered as diesel-electric battery hybrids as a starting point, with options for further emission reduction installed or prepared for. Being technology and supplier-neutral, Ulstein can guide the client to the most suitable fuel and power conversion technology for their business case, taking into account project-specific requirements, supply chain considerations and the vessel's operational profile.
The first contract was signed with Acta Marine on 2 (+2) CSOV TWIN X-STERN vessels in 2022, and several more followed for other shipowners.
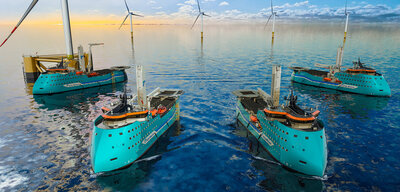
The final step: Decommissioning and repowering
At some point, an offshore wind farm has reached its mission, and decommissioning is needed. In other situations, the choice can be to replace installed turbines with new, larger and more efficient units.
Our substructure installation and commissioning vessels will also be deployed during this last phase of the offshore wind energy life cycle.
Offshore wind production has increased ten-fold from 2010 to 2020, a continuing trajectory.
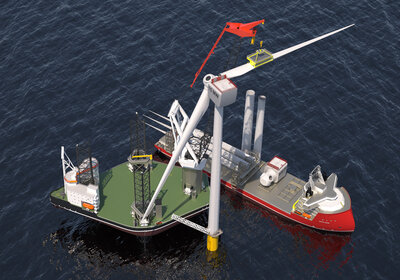
We are innovators - challenge us!
The vessel designs and solutions mentioned here are examples of what Ulstein can do for you in offshore wind. We are thinking differently to make the industry even more competitive.